The Ultimate Guide to Packaging Device Repair Service: Maintain Your Procedures Running Efficiently
In the world of product packaging, the performance of procedures pivots significantly on the reliability of machinery. Understanding the complexities of packaging device fixing is crucial for maintaining optimum efficiency and decreasing disturbances. Normal upkeep not only prolongs the life of these devices however also addresses common issues that can restrain performance. As we discover the subtleties of troubleshooting and the vital decision-making process between repair and substitute, it ends up being clear that a positive method can yield significant advantages. What particular techniques can organizations apply to guarantee their packaging operations continue to be undisturbed?
Relevance of Routine Upkeep
Routine upkeep of packaging equipments is important for guaranteeing optimum performance and long life. By executing an organized maintenance timetable, operators can determine possible problems prior to they escalate right into significant issues. This aggressive method not just reduces downtime however also prolongs the life-span of the equipment, eventually leading to decreased functional costs.
Routine examinations allow for the evaluation of essential elements such as seals, belts, and sensing units. Dealing with damage promptly avoids unforeseen failings that can disrupt production and cause pricey fixings. Additionally, routine maintenance assists make certain conformity with industry standards and policies, promoting a risk-free functioning atmosphere.
Furthermore, maintenance activities such as calibration, lubrication, and cleansing significantly enhance device effectiveness. Enhanced performance translates to consistent product quality, which is important for maintaining customer fulfillment and brand name track record. A well-kept product packaging device operates at optimal speeds and reduces product waste, adding to general efficiency.
Common Product Packaging Equipment Concerns
Product packaging devices, like any complex equipment, can run into a range of typical issues that might prevent their performance and efficiency - packaging machine repair. One widespread trouble is inconsistent sealing, which can bring about item putridity and wastage if plans are not appropriately sealed. This often arises from misaligned elements or worn securing elements
An additional regular issue is mechanical jams, which can take place because of foreign things, worn components, or incorrect alignment. Jams can trigger delays in manufacturing and increase downtime, inevitably impacting overall efficiency. Additionally, digital malfunctions, such as failing in sensors or control systems, can interfere with operations and lead to unreliable measurements or unpredictable machine habits.
Furthermore, concerns with product feed can likewise arise, where products might not be delivered to the product packaging area constantly, causing disruptions. Wear and tear on belts and rollers can lead to suboptimal performance, needing prompt attention to stop more damage.
Comprehending these typical concerns is vital for preserving the honesty of product packaging operations, making sure that equipment runs efficiently and efficiently, which consequently assists in conference manufacturing targets and maintaining product high quality.
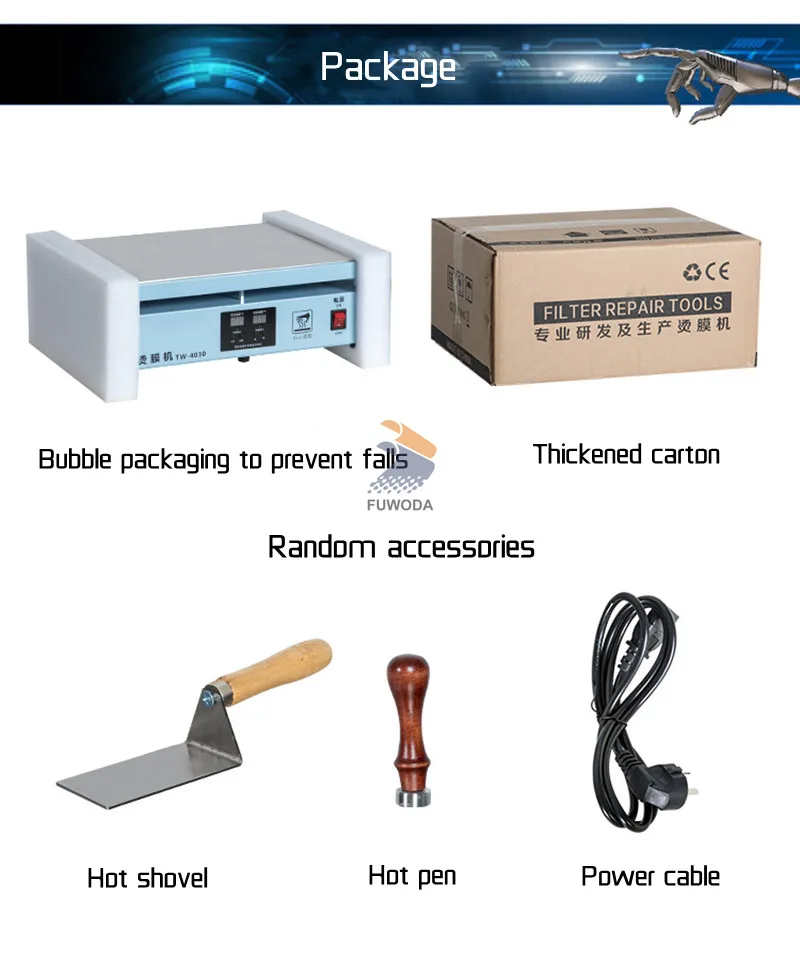
Troubleshooting Strategies
Efficient troubleshooting strategies are necessary for quickly addressing concerns that occur with product packaging makers. A systematic strategy is crucial for identifying the source of breakdowns and reducing downtime. Begin by collecting information concerning the signs observed; this might include uncommon noises, functional More Help delays, or mistake codes presented on the device's user interface.
Following, refer to the machine's guidebook for fixing standards particular to the version concerned. This source can give important understandings into typical concerns and recommended analysis actions. Utilize aesthetic inspections to look for loosened links, worn belts, or misaligned elements, as these physical variables commonly add to operational failures.
Carry out a procedure of elimination by testing private equipment functions. As an example, if a seal is not creating appropriately, evaluate the sealing device and temperature level settings to identify if they satisfy functional requirements. Paper each action taken and the outcomes observed, as this can assist in future repairing efforts.
Repair vs. Replacement Decisions
When confronted with equipment breakdowns, determining whether to replace a packaging or repair equipment can be a facility and essential selection. This choice hinges on several key factors, consisting of the age of the maker, the degree of the damage, and the projected influence on functional effectiveness.
To start with, consider the equipment's age. Older devices might need even more frequent fixings, leading to higher collective costs that can exceed the investment in a new device.
Operational downtime is an additional essential factor to consider. Spending in a new device that uses enhanced efficiency and dependability could be more prudent if fixing the equipment will cause extended hold-ups. Furthermore, think about the accessibility of components; if substitute components are hard to find by, it might be extra strategic to replace the device completely.
Inevitably, performing a cost-benefit analysis that includes both immediate and long-term implications will aid in making an informed choice that straightens with your functional objectives and financial constraints. (packaging machine repair)
Safety Nets for Long Life

Trick safety nets include regular lubrication of relocating components, placement checks, and calibration of sensors and controls. Establishing a cleaning routine to eliminate particles and impurities from equipment can dramatically reduce wear and tear (packaging machine repair). Furthermore, keeping an eye on functional specifications such as temperature level and resonance can assist find abnormalities beforehand
Educating team to identify indicators of wear or breakdown is one more vital part of preventative upkeep. Equipping operators with the understanding to carry out basic troubleshooting can lead to quicker resolutions and minimize functional disturbances.
Documents of upkeep activities, including solution documents and assessment searchings for, promotes accountability and facilitates educated decision-making pertaining to repair services and replacements. By focusing on safety nets, businesses can guarantee their packaging devices run at peak efficiency, ultimately leading to raised efficiency and reduced functional expenses.
Conclusion
To conclude, the efficient repair and maintenance of packaging machines are extremely important for sustaining functional effectiveness. Regular upkeep mitigates visit this web-site the threat of common concerns, such as inconsistent securing and mechanical jams, while systematic troubleshooting strategies help with punctual resolution of malfunctions. Furthermore, cautious factor to consider of repair work versus substitute decisions adds to affordable monitoring of resources. By implementing safety nets, companies can boost machine durability and make certain continuous efficiency in product packaging operations.
Understanding the complexities of packaging machine repair is important for preserving ideal efficiency and decreasing disturbances.Normal upkeep of product packaging machines is crucial for guaranteeing ideal performance and longevity.Packaging devices, like any complex machinery, can encounter a variety of common concerns that might prevent their efficiency and effectiveness. If repairing the device will cause long term hold-ups, investing in a new machine that offers boosted performance and dependability may be much more prudent.In verdict, the reliable maintenance and repair work of packaging equipments are vital for useful source sustaining operational performance.